At Toyota, Craftsmen Get Hands-On In Search Of Innovation
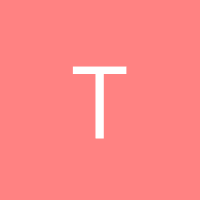
Twenty years ago, as a young Merchant Mariner, I was sent to Japan where the ship I was assigned to, the Sea-Land Spirit, was undergoing a major refit. The ship had begun life as a LASH ship, a vessel that carried cargo-filled barges which it offloaded from its stern via huge, rail mounted cranes that ran on tracks down the length of its deck, and now, after the demise of that business model, it was being converted it into a container ship.
Prior to the refit, the ship had been virtually abandoned, left to rot in some bayside backwater for many years, and it had taken a pounding from the elements. To get it back into service, the ship was towed to Korea where it underwent most of the major modifications, after which it was then taken to the giant Mitsubishi works in Kobe, Japan for the final touches. It was there, so I was told, that Japanese laborers called into question the quality of the Korean’s work. Some of the massive steel braces that had been welded to the deck, they found, were as much as a centimeter off. Shocked by the poor quality of their counterparts’ work, the Japanese shipyard workers cut the braces off the deck, moved them a fraction of an inch and welded them down again.
Photo courtesy of cdn2.shipspotting.com
The Japanese have a reputation for doing things right. Who else could take an iron ore of questionable quality and forge it into blades renowned for their strength, flexibility and sharpness? Who, but the Japanese, could take a pasty skinned, round face little girl and turn her into an object of enduring sexual desire? All cultures make things, but it is only in Japan that the making of things, “monozukuri” is elevated into an art unto itself, and where skilled craftsmen, who spend their entire lives honing their craft to perfection, become “gods.”
In recent years, however, thanks to the amount of production that has been handed over to robots, the number of “gods” on the factory floor has dwindled. Toyota, in particular, has noticed the problem and, according to a recent Bloomberg article, the company if now taking steps to reverse what it sees as a new form of brain drain by taking jobs away from robots and giving them back to men. The logic is slyly simple but infinitely deep, craftsmen, it goes, will always look for ways to innovate, always seek out easier more efficient methods and even find ways to reduce waste while robots can only do what they are programmed to do.
Over the past three years, the article continues, Toyota has introduced more than 100 “manual-intensive” workplaces at factories all around Japan. In one of the sections, men manually turn and hammer red hot steel as it is forged into crankshafts in much the same way that Henry Ford’s workers once did. True to form, the men in the section have been watching and learning and the result of their efforts has been a 10 percent reduction in material waste and a shortening of the production line that will soon be applied to the automated processes used to make crankshafts in the next generation Prius Hybrid.
There is no doubt that the robots are here to stay, but Toyota’s recent experiments show that keeping humans closely engaged in the process can pay real dividends. By empowering workers and encouraging them to become skilled craftsmen who truly understand what it takes to build cars, Toyota is setting the stage for innovation. It is, I think, a uniquely Japanese solution but it could be applied here in North America as well. Despite the many people who decry the lack of skills and poor work ethic of the North American factory worker, I believe that there are a great many men and women in our factories who would jump at the chance to work harder. Everyone, I think, wants to be valued and most people want to make a difference. This could work here too, maybe some of our own best and brightest should take a look at what’s going on.
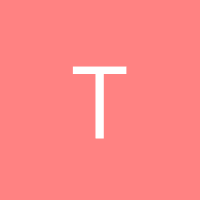
More by Thomas Kreutzer
Latest Car Reviews
Read moreLatest Product Reviews
Read moreRecent Comments
- Amy I owned this exact car from 16 until 19 (1990 to 1993) I miss this car immensely and am on the search to own it again, although it looks like my search may be in vane. It was affectionatly dubbed, " The Dragon Wagon," and hauled many a teenager around the city of Charlotte, NC. For me, it was dependable and trustworthy. I was able to do much of the maintenance myself until I was struck by lightning and a month later the battery exploded. My parents did have the entire electrical system redone and he was back to new. I hope to find one in the near future and make it my every day driver. I'm a dreamer.
- Jeff Overall I prefer the 59 GM cars to the 58s because of less chrome but I have a new appreciation of the 58 Cadillac Eldorados after reading this series. I use to not like the 58 Eldorados but I now don't mind them. Overall I prefer the 55-57s GMs over most of the 58-60s GMs. For the most part I like the 61 GMs. Chryslers I like the 57 and 58s. Fords I liked the 55 thru 57s but the 58s and 59s not as much with the exception of Mercury which I for the most part like all those. As the 60s progressed the tail fins started to go away and the amount of chrome was reduced. More understated.
- Theflyersfan Nissan could have the best auto lineup of any carmaker (they don't), but until they improve one major issue, the best cars out there won't matter. That is the dealership experience. Year after year in multiple customer service surveys from groups like JD Power and CR, Nissan frequency scrapes the bottom. Personally, I really like the never seen new Z, but after having several truly awful Nissan dealer experiences, my shadow will never darken a Nissan showroom. I'm painting with broad strokes here, but maybe it is so ingrained in their culture to try to take advantage of people who might not be savvy enough in the buying experience that they by default treat everyone like idiots and saps. All of this has to be frustrating to Nissan HQ as they are improving their lineup but their dealers drag them down.
- SPPPP I am actually a pretty big Alfa fan ... and that is why I hate this car.
- SCE to AUX They're spending billions on this venture, so I hope so.Investing during a lull in the EV market seems like a smart move - "buy low, sell high" and all that.Key for Honda will be achieving high efficiency in its EVs, something not everybody can do.
Comments
Join the conversation
"By empowering workers and encouraging them to become skilled craftsmen who truly understand what it takes to build cars, Toyota is setting the stage for innovation." That's actually highly risky if the business model is dependent upon a lot of skilled craftsmen. A good business model requires an ability to execute it effectively. Toyota designed its lean system so that people who had fairly average skills could be trained to do whatever jobs that were needed. Not quite as mindnumbing as Ford's version of mass production, but not retro, either. Setting up a high-volume production line that is dependent upon heroes for its success is pretty much begging for failure. I suppose that the downside of machines must be that it is more difficult to maintain continuous improvement, since the machine doesn't learn anything and then relay the lessons learned. Perhaps this approach finds a balance that involves just enough humans that the machines can get the help that they need.
These 'craftsmen' must have been on vacation the week the 2015 Camry front end was designed and approved.