Tesla Model S Customer Blog: Beta Under The Bright Lights
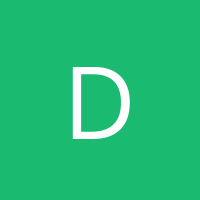
[Editor’s note: videos are from Youtube, and were not taken by the author]
“THE BETAS ARE COMING!” The mid-August e-mail from Tesla Motors breathlessly touted “the most exciting automotive event of the year:” an exclusive owners-only unveiling of the Model S. All 6,000 of us who’d put down $5K deposits on the electric sedan would be invited out to Tesla’s sprawling new plant in Fremont, Calif. to see, touch, and ride in the Beta version of the car, described as “over 90 percent production intent.”
A few weeks later came the e-mail invitation itself. I RSVPed the same day. Tesla had expected attendance in the hundreds, and had made initial plans for 1,000 just to be safe. But when 300 RSVPs came back in the first 23 minutes, they realized they had a tsunami of customer enthusiasm on their hands. In the end, about 2,000 owners showed up, including one guy from Kazakhstan.
Driving my rented Prius up I-880 toward Fremont on the big day, I passed a factory with huge letters on the side: SOLYNDRA. Not a good omen. The start-up Silicon Valley manufacturer of high-tech cutting-edge solar panels, the recipient of half a billion dollars in government loans, had lost hundreds of millions of dollars and just gone bankrupt amid cries of political favoritism and financial fraud.
A mile or so up the road, another sprawling factory festooned with giant letters: TESLA. A start-up Silicon Valley manufacturer of high-tech cutting edge automobiles, recipient of half a billion dollars in government loans, currently reporting annual losses of hundreds of millions of dollars….oh, never mind.
Dozens of BMWs in the parking lot, a Panamera here, a tricked-out Lotus there. Up by the door, a half-dozen Roadsters tethered to their charging stations. I join the stream of owners, chattering excitedly, as we walked up a literal red carpet to the factory entrance. The first thing we see inside: a Tesla boutique selling logoed shirts, jackets, and accessories. Business is brisk
Then down a long hallway formed by temporary white walls that mask the stunning vastness of the plant, the former NUMMI factory owned by Toyota and GM. Then, bang, we’re in the middle of it, shiny white floors that stretch out almost to the limits of vision, with bright red robotic machinery scattered about, and several Model S prototypes staged in various points of assembly. Over to the right a dark corner of the plant, maybe half a football field in size, has been set up like a night club–leather couches and tables, potted plants, open bars, hors d’oeuvres at every turn, dim blue and red lighting, pulsating club music.
Wine in hand, and resisting the entreaties of a black-clad waiter offering bacon-wrapped scallops, I chat with another owner, lamenting the fact that the earliest slot I could get for a ride was 10:30 p.m., five hours from now. He’s scheduled for a ride in a few minutes, and offers to let me stand in for his no-show guest.
Waiting in the ride line, we watch the three ride cars–one black, one white, one red–come and go with their cargoes of four riders. Each arrival looks like a NASCAR pit stop: the car screeches up, two Tesla employees attack the car with polishing rags while three others open the doors and shoo out the grinning passengers. Four new riders, carefully prepositioned for quick entry, are then ushered in, and the car tears off once more. Elapsed time, maybe 30 seconds.
At last, my turn. I get shotgun, and at 6 feet 2 I find the front seat a bit cramped because it’s pulled forward for more legroom in back. I’m barely buckled in and have just glanced at the huge center video screen before we race off into the empty back parking lot. First up is a short slalom course, to demonstrate the flat cornering, the result of the heavy, low-mounted battery. “Lowest c.g. in the business,” the driver intones. Then a couple of quick turns, and we line up for a quarter-mile straightaway.
We accelerate briskly to about 65 mph in almost total silence. I ask the driver to back off the accelerator abruptly at high speed, so I can get a feel for the regenerative braking. (In a brief test drive of the Roadster a couple of years back, I found its abruptly powerful trailing-throttle regen to be way too much for everyday driving. Hopefully the S would feel more like a normal car.) He obliges, and I’m relieved that, from the passenger’s point of view at least, it seems pretty normal. No lurch against the shoulder harness.
One more quick 180, another brief spurt, and we’re back at the start. The doors fly open, and the next four riders surge forward. Total elapsed time: 90 seconds.
I refill my wine glass, load up on Thai noodles, and start looking for Tesla engineers. There are dozens of them scattered around, each clad in a grey polo shirt, each eager to talk. By luck, one of the first I introduce myself to is Drew Baglino, who happens to be directly involved in setting up the Model S regen braking system.
He has some surprises for me. First, he tells that the regen profile of the Model S is precisely the same as the Roadster. So why did it feel different to me? For one thing, I tested the Roadster in New York City, and never exceeded 50 mph. On both cars, the regen is set to be stronger at low speeds, so I was comparing 40-mph regen on the Roadster to 65-mph regen on the Model S. Moreover, the extra 500 lbs of passengers in the S would have reduced the S’s deceleration.
He also countered my impression that the Model S’s braking system–in which the brake pedal actuates only the standard friction brakes–is less efficient than the blended system of the Toyota Prius, in which the brake pedal initially activates the regen system, resorting to the friction brakes only when additional brake force is needed in abrupt stops.
“Tesla’s brake system is just as efficient as Toyota’s, and we’ve done the dyno testing to prove it,” says Baglino. What’s not widely known, he says, is that the Toyota system does indeed apply the friction brakes slightly whenever the brake pedal is used. This smooths the transition to full friction braking when necessary.
When I pleaded for driver-adjustable regen on the Model S, he said this was under consideration. (Two days after the event, while writing up this report, on a whim I e-mailed Tesla boss Elon Musk and repeated my plea for driver-adjustable regen. Three hours later, I got this reply: “I totally agree that regen should be driver-adjustable and it will be on Model S.” The message was Cced to JB Straubel, Tesla CTO.)
Over by the info/nav/audio system display, a battery engineer tells me that the 300-mile version of the S will have a battery capacity of 85 kWh. But he won’t reveal the capacities of the shorter-range versions. But some simple math suggests that the 240-mile version will have 68 kWh and the 160-mile version about 45 kWh. Even the latter is nearly double the capacity of the Nissan Leaf.
There will be about a 220-pound weight penalty for each step up in battery capacity, I’m told. The higher-capacity batteries will have some combination of more cells and improved cell chemistry. Final specs have not yet been determined.
Over by the dessert bar (I can’t resist those mini-eclaires) a charging system engineer shows off the Model S charging plug, which will plug into either 120v or 240v outlets. At 240 volts, the car will charge at a rate of 9.6 kW, enough to completely charge the 300-mile battery in about nine hours. On the average, he tells me, I’ll add 30 miles of range for each hour of charging. An optional second built-in charger will double those charging rates.
As much fun as it is talking to the engineers, at around 8 o’clock, all conversations stop and everyone moves toward an elevated stage at the rear of the main factory bay.
Elon is coming!
Atop the platform, a Tesla marketing exec plays Ed McMahon to Musk’s Johnny Carson, whipping the crowd into a frenzy of anticipation. (Although he didn’t quite shout “Heeeeere’s Elon!) Musk makes his entrance at the wheel of the red Model S, as the crowd cheers and camera strobes flash. Four Tesla employees ride in the passenger seats. Wearing a tuxedo jacket over a checked sportshirt, Musk then walks around to the back of the car and opens the hatch to reveal his 7-year-old twin sons sitting in the rear-facing child seats.
As the seven bask in the cheers of the crowd, another guy climbs out from under the hood. Okay, we get the point: the Model S is pretty roomy.
It’s the first time I’ve seen Musk in person, and I’m surprised that he seems like a pretty normal guy, maybe even a little geeky, a bit hesitant and awkward amid all the fuss. His rock-star reception, it seems, is inspired not by personal charisma, but by the crowd’s understanding of his vision and accomplishments. Musk gives a short, stumbling speech, briefly demonstrates the entertainment system features–like the ability to surf the Internet, which will probably alone double the car’s accident rate–and walks off to thunderous applause.
Immediately, the crowd storms the stage to inspect the car up close. A squad of nervous-looking Tesla guys gently shepherd us off the platform. With the stage finally clear, Ed McMahon drags Musk back on stage. It seems that Elon forgot to make the most important announcement of the evening: that there will be a high-performance version of the Model S that will do zero-to-sixty in under five seconds. More wild applause.
It’s pushing 9 p.m., but there’s still time for a factory tour. Instead of the 15-minute rush job I expected, we get an hour-long dog-and-robot show of virtually the entire production process. (The one exception is the paint shop, which we’re told is a 40-minute walk away. The factory is that big.) What stands out for me are the robots: ranging in size from ostrich to giraffe, bobbing and weaving, clutching, punching, drilling, welding. “These are my toys,” one robotics engineer tells me proudly. “This one here does a fantastic job of welding aluminum, which is a lot harder than welding steel. It’s far better than anyone could do by hand. Every weld is perfect.”
While the production line is by no means complete, and the robotic gyrations we see this night are choreographed primarily to impress the rabble, to the layman’s eye it looks like they could start building cars next month. In my mind, there is little doubt that Tesla will make its production target of mid-2012.
Every Tesla employee I talk to seems to love the place. One production engineer had worked at the plant when it was run by the Toyota/GM patnership. “This was a dirty, nasty place under Toyota,” he tells me. “The floor was black with stuff. Tesla cleaned everything up. Look at the floor now. This place is more like an Intel chip plant than a car factory.”
He also raves about the Tesla operating style. “When I first got here, I was overwhelmed by the opportunities to innovate. It’s such a team-oriented place. Everybody is always bouncing ideas off each other.” Another engineer, the guy in charge of headlights, stells me, “Elon drops by my office to chat every few weeks. He likes to know what’s going on.”
Now it’s nearing 10:30, the time for my official ride. This time I sit in back, the right window seat. This driver seems more enthusiastic than the first one; he slams through the slalom course, chuckling “This should help you folks in back get to know each other better.” The acceleration run seems more aggressive, too, and we hit almost 80 mph as the floodlit cones approach in the windshield. A couple of the passengers actually scream in delight, as if riding a roller coaster.
Is it all too good to be true? Have I been hoodwinked by the shiny prototypes and the mini-eclaires and the rock-star CEO? Maybe. But I’ll be very surprised if Tesla meets the same fate as Solyndra just down the road. Despite the doubts of my wife and a few friends, I’m confident that my $5,000 deposit is in good hands. And I really, really want that car.
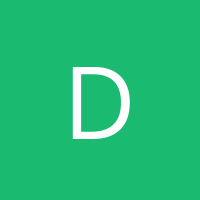
More by David Noland
Latest Car Reviews
Read moreLatest Product Reviews
Read moreRecent Comments
- El scotto Dale Carnegie had his grandkids do some upgrades?
- El scotto Work it backwards. How many people use Tesla Super Chargers: Primary Charging Point - this is my normal charging station; Secondary charging station - at a retail location or planned on trips, Rarely or Not at All.
- FreedMike Some clarification would make sense here: Tesla is laying off the team responsible for BUILDING NEW Supercharger stations. Apparently the ones already being built are going to be completed. The folks who maintain the current network are apparently unaffected. https://www.nytimes.com/2024/04/30/business/tesla-layoffs-supercharger-team.htmlAlso, many other other manufacturers are switching to NACS in the upcoming years, and some of those companies are already providing Supercharger adaptors for their non-NACS vehicles. Some Superchargers can already accomodate non-Tesla vehicles with a built in adaptor called the "magic dock."Given all this, my guess? They're trying to maximize utilization of the current system before building it out further.
- Dartman Damn Healey! You can only milk a cow so many times a day! Don’t worry though I bet Flex, 28, 1991, and all the usual suspects are just getting their fingers warmed up!
- FreedMike Your Ford AI instructor:
Comments
Join the conversation
Beautiful car; I want one.
"At 240 volts, the car will charge at a rate of 9.6 kW" Only if you have a 40 Amp circuit. And don't use the clothes dryer or the toaster while that is going on.