EXCLUSIVE: Bernstein's MQB Report In Full
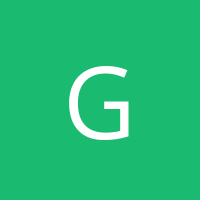
Despite a chorus of largely uncritical reporting, there is a growing contingent of those who question VW’s claim that their new MQB modular architecture will bring about significant savings. The latest among them is Bernstein Research. A report by noted analyst Max Warburton ( who recently authored the definitive study on Chinese cars) questions VW’s claims and shows how MQB may be helpful, but not nearly as significant as VW claims. On the other hand, it’s worth noting that these reports are meant for end-user investors, not necessarily industry types.
In theory, the MQB platform is a dream come true for any auto manufacturer, allowing a one-size-fits-all platform to span across their expansive product offerings and further increase economies of scale by offering both standardization and flexibility all in one neat package. From that perspective, it’s easy to wonder “how can Volkswagen NOT save money?” And for a company like VW, which is arguably an industry leader in scale, 20 percent might even be an appropriate figure.
Like any prudent business student, I began to question the numbers being disseminated from the company. 20 percent seemed too neat, too easy, and most of all, too tailor made for a largely unquestioning automotive press. My thoughts trailed back to my introductory finance class. One key consideration that should be taken into mind when analyzing company valuations is the optimism of those responsible for creating the financial models. Naturally, I figured 20% was the result of this phenomenon. If you think about it, it’s tough to imagine, “VW Announces MQB to Save 2% of Costs,” making a splash in the headlines.
Bernstein Research’s analyst report on MQB presents a more contrarian view. Overall, Bernstein was unimpressed with MQB, claiming that the benefits were “over-hyped.” This viewpoint had differed so drastically from my initial research on modular platforms, which hailed them as the next wave of change and innovation in the automotive industry. How could this gap be reconciled?
To fully understand and appreciate the report, I had to get into the mind of its intended end-user, an investor. The mindset of an investor is much different than that of a car enthusiast. While industry observers herald MQB as the next great leap forward for automotive manufacturing, an investor cares about one thing and one thing only: money. From an investor standpoint, if MQB cannot deliver any value though its stated cost savings and result increase company earnings, it is largely irrelevant.
The report states, “There may be some savings from this [MQB], but they are likely to be very modest.” [1] The modest nature of these savings stems from a number of sources. First, MQB does not help to lower a manufacturer’s major costs like raw materials, labour, and assembly hours. Remember that economies of scale, at its core, is the ability for a business to save money by spreading its fixed costs across a higher volume of production. This definition would lead to the assumption that by standardizing all of its platforms, VW will be able to cut costs throughout the supply chain by having their suppliers reach economies of scale. However, the report argues that past a production level of 1 million units, there begins to be diminishing returns.
Bernstein explains, “scale economies are usually exhausted at the plant level rather than the firm level.” [2] Since most OEMs are already at full scale, they already purchase parts from suppliers in some sort of economic batch size. In order for suppliers to save through economies of scale, they would have to increase their production. Since suppliers are also already at full scale, they would have to increase the capacity of their plants in order to increase their output. The capital expenditure related to increasing capacity, whether it is machines or labor, effectively negates any sort of cost saving that was originally sought after.
Theoretically, if VW sourced its parts and raw materials from one centrally located monster plant, it would be much easier to realize these savings. VW’s geographical diversification and localized sourcing makes this much harder to achieve, as each separate location has its own associated fixed costs. Think about it in terms of trying to house all of your cars in one mega garage, or in 10 separate garages across the city. The one mega garage has a single set of maintenance and utilities, which the latter option has 10.
A more grounded figure for MQB’s cost savings is somewhere in the neighborhood of 2%-5%, similar to what Renault-Nissan claimed. As mentioned above, 2% is not the most attractive number to unveil to the public, but this relatively small figure should not be dismissed completely. VW’s costs of sales were over 157 billion euro in 2012. A 2% cost saving would translate to an additional 389 million euro in earnings before interest and taxes, or an addition of 0.83 euro on a per share basis. Even on the lower end of estimations, it is clear that if MQB can help lower costs by any amount, it still helps to deliver value to VW and its shareholders. If you were to put $389 million in my pocket, I wouldn’t be too upset.
When considering the competitive nature of the automotive industry and the resulting intense margin compression that manufacturers face, the amount of cost savings are even more impressive. I like to think about it in terms of a Formula 1 race, in which the shaving of even a few milliseconds off of a car’s lap time is a huge accomplishment. Success is relative, and numbers, whether they be tenths of a second or percentage points, are meaningless without context.
Even if savings derived from MQB are under 2%, let alone 20%, it still provides a huge strategic advantage for a multinational auto manufacturer like VW. The ability to remain flexible across its product offering will allow VW to continue to serve existing and emerging markets, each with its own specific needs. It will be interesting to see if VW can effectively leverage MQB’s capabilities in its implementation. The ability to “flex” plants quickly (from a Golf to a Tiguan for example) based on market demand is one aspect that has been barely mentioned, but could prove to be a significant advantage.
Graeme Kreindler is an HBA Candidate at the Richard Ivey School of Business at The University of Western Ontario.
TTAC thanks Max Warburton and Bernstein Research for providing the report.
References
[1] Pg 30
[2] Pg 24
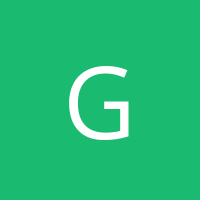
More by Graeme Kreindler
Latest Car Reviews
Read moreLatest Product Reviews
Read moreRecent Comments
- Peter Buying an EV from Toyota is like buying a Bible from Donald Trump. Don’t be surprised if some very important parts are left out.
- Sheila I have a 2016 Kia Sorento that just threw a rod out of the engine case. Filed a claim for new engine and was denied…..due to a loop hole that was included in the Class Action Engine Settlement so Hyundai and Kia would be able to deny a large percentage of cars with prematurely failed engines. It’s called the KSDS Improvement Campaign. Ever hear of such a thing? It’s not even a Recall, although they know these engines are very dangerous. As unknowing consumers load themselves and kids in them everyday. Are their any new Class Action Lawsuits that anyone knows of?
- Alan Well, it will take 30 years to fix Nissan up after the Renault Alliance reduced Nissan to a paltry mess.I think Nissan will eventually improve.
- Alan This will be overpriced for what it offers.I think the "Western" auto manufacturers rip off the consumer with the Thai and Chinese made vehicles.A Chinese made Model 3 in Australia is over $70k AUD(for 1995 $45k USD) which is far more expensive than a similar Chinesium EV of equal or better quality and loaded with goodies.Chinese pickups are $20k to $30k cheaper than Thai built pickups from Ford and the Japanese brands. Who's ripping who off?
- Alan Years ago Jack Baruth held a "competition" for a piece from the B&B on the oddest pickup story (or something like that). I think 5 people were awarded the prizes.I never received mine, something about being in Australia. If TTAC is global how do you offer prizes to those overseas or are we omitted on the sly from competing?In the end I lost significant respect for Baruth.
Comments
Join the conversation
Graeme you can do better! Look at the info th009 provides. Thanks btw for the extra info! I'm skeptical at the 20%, that is based as I understand on the manufacturing costs. My skepticism is mostly based on what Graeme points to: it sounds to nice. On the other hand I have to dig through the Bernstein report and the extra info from th009. According to Graeme's calculation the manufacturing costs at VW are: 389 million/2%=19.45 billion So manufacturing costs are 19.45/157=1.23% of the total costs of sales. Hmmmm, numbers numbers. What about cutting manufacturing costs by producing in a country where the currency is low and just ship your cars to where the markets want them?
Robots. If the frame is standardized there is no need to reprogram and/or reposition any robotics involved in assembly.